Articles by: Ankit Patel
10/20/09 by Ankit Patel | Uncategorized | No Comments »
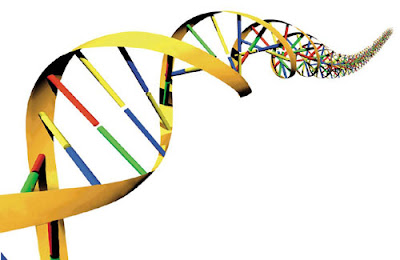
Competition is what business in a free market is all about. Wouldn’t it be great if we have a competitive advantage that our competition couldn’t duplicate? The question becomes what do you have that our competition does not? The culture of a company is a distinctive and unique advantage. Think of it like DNA or a fingerprint but for a company. You want to be sure that you foster the right culture that will give you an advantage; here are 5 ways to do that:
1) Empower Employees. One of the most underutilized resources we have is our people. The people who work any given process are usually the ones best for solving its problems.
2) Train, Train, Train! If you’ve empowered your workforce then you need to make sure they are resolving problems correctly and are staying sharp. Having a robust training program lets us make sure everyone is aligned on how we solve problems and it also keeps them knowledgeable about the latest and greatest techniques and information.
3) Policy Deployment. If you have everyone working on fixing problems you want to make sure they are all aligned.
4) Think Like a Profit Center and Not a Cost Center. Many times we make decisions based on the fact we are just running an operation. If we start thinking like we are a self contained business then are decisions become different. Instead of cutting cost we look at how we can generate revenue.
5) Learn from Others. It is helpful to benchmark your performance to others in the industry as well as look at operations in other industries. By benchmarking we get more ideas get another company’s perspective on an issue.
These tips are just a starting point but ultimately they will help us obtain a culture that no one else can duplicate, a culture that is always looking for more efficiency and revenue opportunity. The transition to this state is not easy but with support, determination, and discipline it can be achieved.
10/14/09 by Ankit Patel | lean, lean culture, lean manufacutring, lean transformation, standard work, the lean way consulting | No Comments »
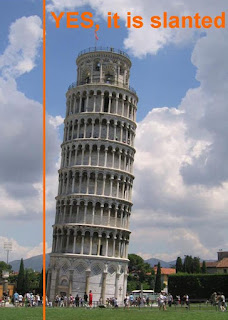
Most everyone knows about the leaning tower of Pisa but why did it get that way? This is straight from Wikipedia – “The tower began to sink after construction had progressed to the third floor in 1178. This was due to a mere three-meter foundation, set in weak, unstable subsoil, a design that was flawed from the beginning.” If they had standard design and construction processes these disasters may have been avoided. Standard work might have saved one of the most famous Italian monuments. This instance we have something “interesting” from not following standard work but normally that is not the case.
What is Standard Work? Standard Work is a way to have a duplicatable and repeatable process that is improvable. Standard Work gives you consistency and if done correctly it gives a tool to systematically improve your processes. Here are some examples where Standard Work is important:
• Nuclear Reactor
• Airplane Pilot
• Airport Traffic Control
• Driving
• Any manufacturing or service process
Most people think Standard Work is work instructions but that is only affects the first 2 parts of repeatable and duplicatable. Here are some items you want to include when doing Standard Work and the category that they fall into:
There are other tools but these are a good starting point. Does your organization do the above listed tools? If you are not using the tools listed above are you really doing Standard Work? Short answer is probably not! Why spend the time implementing standard work? “Where there is no Standard there can be no improvement” – Taiichi Ohno (Founder of Toyota Production System). Standard Work is a corner stone for making improvements in your organization. You may see improvements with new process designs but those improvements will not continue unless there is robust Standard Work in place to allow for predictable changes. Not only will you continue to improve your organization but you will do it in a systematic and deliberate.
10/12/09 by Ankit Patel | lean, lean culture, lean fail, lean manufacutring, lean transformation, the lean way consulting | No Comments »
Today’s title was the phrase that was told to me when I first started in my lean journey during a transformation process.
When going through a lean implementation there are two aspects we look at:
1) Technical and tangible aspects
a. Design elements
b. Scheduling
c. Staffing
d. And other tools
2) Non-technical and intangible aspects
a. Culture
b. Morale
c. Willingness and ability to change
Often times we put most of our effort into the tangible items because we feel since we can “touch” these items we can have greater impact on our change. With Lean, culture is the main driver of impact. Any change made will be temporary unless your culture changes. You’ll spend the majority of your time (initially) working on the tangible aspects but your impact really comes from cultural changes:
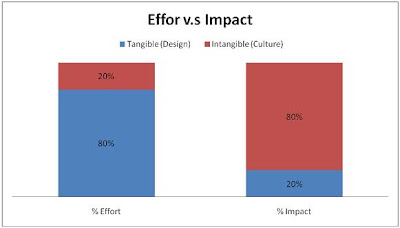
The reason culture is so important is that with Lean the people are equally integral to process as any piece of machinery or process. Solutions are driven not just from management/engineering to the floor but the people running the process on a daily basis are empowered and responsible for fixing process issues. Improvement isn’t viewed as a process with bureaucracy; improvement is just the way we do businesses. An example would be instead of organizing Kaizen events three weeks out and then having follow-up meetings to sustain the events we would have a suggestion, pull the team together to implement and continue to run the business with the new change in place.
The next question becomes how do we focus more on culture? Changing the culture is like losing 100 pounds. It takes time and effort and you will not see overnight results. Here are some things that can be done to make the cultural transition easier:
Train, Train, Train
-Training people on how to do and implement Lean will help everyone be on the same page and make improvements easier to manage
Change the metric
-People respect what you measure
-You want to measure the right metrics and hold people accountable to team metrics and individual metrics
Management needs to support the new culture
-Managers are integral to making a Lean culture work. The more the managers support and practice Lean principles the likelier the success of a Lean program.
10/10/09 by Ankit Patel | lean, lean manufacutring, lean transformation, muda, mura, muri, the lean way consulting | No Comments »
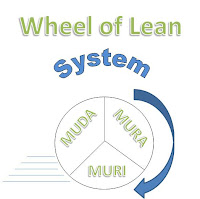
Many of us at are familiar with the seven wastes:
Transportation
Inventory
Motion
Waiting
Over processing
Over production
Defects
Too many companies focus on just the above 7 when they are only 1/3 of the issues in a system. TIM WOOD is called MUDA. There are 3 elements that need to be addressed when making a system lean:
· Muda – Activity that is wasteful and doesn’t add value or is unproductive
· Mura – Unevenness/inconsistency in a process and “flow” of the product
· Muri – Overburdening
Muda is easy to see and is the type of waste that gets most the emphasis when it comes to Lean. Muda is not more or less important than the other two wastes. Examples of Muda include operators standing around because they are waiting on the operation before them to finish, a quality hit, or having too much raw material.
Mura means unevenness. You can think of Mura as flow. Do systems/invoices/product flow through a process? Is there regularity of the flow? Is the flow predictable? Typically you address flow issues with a kanban(s) and create a pull system.
Muri means overburdening. The expression “running like a chicken with its head cut off” is a good way to describe Muri. Muri also refers to overburdening in work content and ergonomically. How often have you felt there was too much work to get done in a normal 40 hour week? Is there an area of work that causes repeated ergonomic issues? The way to address Muri is through standard work and safe ergonomic practices and designs.
Think of Muda, Mura, and Muri as equals; they are all parts of a wheel and they all have to be balanced to make the wheel turn. You’ll go much farther and faster when your wheel is even and smooth.
10/08/09 by Ankit Patel | company culture, lean, lean culture, lean fail, lean manufacutring, lean transformation, the lean way consulting | No Comments »

Thank you to www.shmula.com for the photo and an interesting article why lean transformations fail. Thank you also to Henry Ford for the title of today’s blog post.
The picture tells a very interesting story. 70% of transformations fail because of ourselves. We are are worst enemies when it comes to change. None of use are really a stranger to the concept, how many times have we told ourselves “I shouldn’t eat that” or “I’ll do that work next week.” My personal favorite is “I like it the way I’m doing now!”
The reality is that the actual bolts and nuts of a lean transformation are the easy part. The hard part is looking into the company mirror and asking “is my company going to make it through the transformation.” From experience I know that whatever you think you can do is what you will do. The main question with a transformation really becomes how do I make sure I’m culturally ready for a transformation.
The truth is that there is no 1 right way but there are some rules of thumb that you may want to follow.
1) Upper and middle management must be on board and understand how to be lean managers
2) Your metrics will dictate behavior. Change your metrics to make your lean transformation successful.
3) Never stop training or you may regress on the progress you’ve made
4) Have a beacon (aka lean sensei) that will be your guiding light and voice of reason through a transformation and beyond
5)Reward good behavior and ignore (and in some special cases punish) bad behavior.
6) Stay the course.
These guidelines will help you through your journey. BON VOYAGE!
10/06/09 by Ankit Patel | lean, lean manufacutring, root cause, the lean way consulting | No Comments »
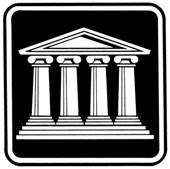
Like many of you I’ve been hearing a lot about the health care debate and it got me thinking. Now I know there are many sides to the problem but I think the one question we have to ask ourselves is “What’s really the problem?” When I think about it I realize that 32% of people in the U.S. are obese and obesity leads to cardiovascular disease, certain types of cancer, and type 2 diabetes. So I ask you is the problem with the health care system or is it in our food supply and our health & nutrition education?
That is an oversimplification of the problem but if you think of any problem/issue as a building with pillars/supports. If you want to demolish the house you could just blow up the foundation and that would take care of the your problem. The same is true for fixing the root cause for a problem. Fix the root cause and all your other related problems will disappear. You can also remove several of the supports and accomplish the same goal but it may not be as clean of a demolition and you may still have standing parts of the structure. This usually happens when we fix issues not realizing (not not willing to realize) they are part of the same problem.
Fixing the root cause is always the best solution but there are a couple of issues:
1) You have to understand the problem enough to find the true root cause
2) It can be impractical/impossible at times to change the root cause
3) It takes a long time to change the root cause and you need a temporary solution in the mean time.
Back to our health care question:
1) Do we understand the problem enough? I would say not really. The food supply/nutrition education is just one aspect of the root cause. We would have to ask deeper questions like why is our food supply the way it is and why we don’t have better nutrition education.
2)Is it impractical or impossible to fix the root cause? My personal feeling is that there is no problem that is impossible but some that might be impractical so that’s when we get to the 3rd point
3) Changing the food supply and education system would take a long time so as a temporary fix we could give everyone health care which is the solution being prosed.
Unfortunately what usually happens when we put in a temporary fix is that we don’t “see” the problem so it’s out of sight out of mind. Moral of the story, always try to fix the main problem the first time.
10/04/09 by Ankit Patel | lean, poka yoke, poke yoke, the lean way consulting | No Comments »
Well maybe not divine but it sure does help you from making those “human error” mistakes. Ever heard of Murphy’s Law? “Any thing that can go wrong will go wrong.” In short if something has the possibility of happening, it will happen. You can only flip the coin on heads so many times before it tails shows up. The same is true for any possible mistakes someone might make at their job. Eventually if they do it long enough you will make mistakes.
So what can we do to stop all these mistakes from happening before they happen? Poka Yoke, aka error proofing, is a great way to prevent errors.
First off lets take a look at types of Poka Yokes.
1) Signal or a sign to help prevent the error
2) Physical barrier or tool to help with a task to prevent an error
3) Design the problem out
Example using a rail road crossing and the error is a vehicle getting hit by a train:
1) Having just a flashing light at the RR crossing
2) Having a flashing light and a mechanical arm that comes down to prevent a vehicle from passing
3) Moving the RR above the road where it is completely out of the way of the vehicles
Obviously option #3 is the best solution but it’s not always the most cost effective so we go to the next best thing which is #2 a physical device or barrier to prevent the error. Other examples of a device might include a jig, a specific size hole for a specific product, templates, etc.
I use this in my personal life all the time. I will always leave my house keys on top of my wallet and my cell phone. If I want to leave the house I never forget the house key. If you are child proofing your house you will plug electrical outlets and gate certain areas of the house so the baby won’t wander in to a dangerous room.
Next time you have a defect in your work area just think “What can I do to make sure this never happens again” instead of “Who’s at fault?” You’re work will go much better in the long run.
« Previous Page