Articles by: Ankit Patel
05/17/17 by Ankit Patel | Uncategorized | No Comments »
Asking someone “How was your day” vs asking “What was the best part of your day” will usually get you two very different answers. The usual response to how was your day is at best “fine.” When you ask what was the best part of your day it forces a person to think through and tell you the high part of their day and it elicits different emotions. This sounds great and you might be thinking like I did “Positivitiy is great but how does it help the business other than it’s a nicer place to work?” Being a nice place to work has it’s benefits from reducing turn over to higher engagement of employees. Aside from that there is some research that shows the amount of positive comments to negative comments can affect sales performance directly.
The Role of Positivity and Connectivity in the Performance of Business Teams: A Nonlinear Dynamics Model by Marcial Losada and Emily Heaphy published in American Behavioral Scientist 2004; 47; 740 goes into how positivity influences the bottom line of a business. In this study they took 60 sales teams of an IT sales organization and the company ranked them as high performing, average performing, and low performing teams. For six months they recorded and encoded every group conversation the teams had. They controlled for experience, talent, personnel and a whole host of other items. What they found was that the controlling factor was the ratio of positive comments to negative comments.
High performing teams had a ratio from 3:1 to 9:1
Average performing teams had a ratio of 2:1
Low performing teams had a ratio of 1:3
The conclusion was that the worse the ratio the more of a stress response which dropped the performance of the team. What is the positive to negative ratio for your teams?
If you want to learn more about how to increase the positive to negative ratio in your teams conversations and how to implement it apply for a discovery call now and we can do a deep dive discovery of your situation at no cost if you qualify.
Click to Apply
05/10/17 by Ankit Patel | Uncategorized | No Comments »
This the final post about a change management frame work ATEEP. We’ve covered alignment in Framework for Change Management Part I , team in Framework for Change Management Part II, experimenting in Framework for Change Management Part III, and execution in Framework for Change Management Part IV. The last step is the one that almost no one will pay attention to. That is how to make the changes permanent. Another way to say this is how do you make it a part of the fabric of the company. The usual way to do this is to create meeting, metrics, or other management tools. Usually this is helpful but not enough. To create something as part of your culture you need other items like stories, artifacts, and rewards. A story is simply what gets shared from person to person. It’s important to highlight a story and repeat it so that everyone understand the message. One example of a story is the story of how Google started off in a garage and grew to a giant corporation. Or the story of how the Facebook founder came up with the idea for Facebook. Artifacts are that are usually physical that reinforce the culture you want. An example of this would be t-shirts talking about the non profit that the company supports or even placards that you keep next to your ID badge. With rewards it can be both monetary and non-monetary. Non-monetary rewards can be public praise, highlighting exceptional performance, or even a thank you for doing something related to the change you want.
Keep in mind as you implement any change it’s not going to be easy and it will take effort and time. Any change that is hard won’t be linear and you will take steps backwards and forwards. Keep the ATEEP framework in mind to help you through sticking points.
If you want to learn more about ATEEP and how to implement it apply for a discovery call now and we can do a deep dive discovery of your situation at no cost if you qualify.
Click to Apply
05/03/17 by Ankit Patel | Uncategorized | No Comments »
ATEEP is the framework that we use to help accelerate and make change stick. We’ve covered alignment in Framework for Change Management Part I , team in Framework for Change Management Part II, and experimenting in Framework for Change Management Part III. Once you have your solution execution is next in the change framework. At this point you have to take what you’ve learned and role it out to the entire organization. Now this may sound easy but can be the most difficult part. Especially if you haven’t done the first 3 parts properly. One of the tools you want to use is a RACI. This is a way to determine who is Responsible, Accountable, Consulted, and Informed during the role out process. Another tool you will want to use is a scope document where you highlight was is in scope and out of scope. There are standard project management tools that are very effective if you have the proper Alignment, Team, and Experiments that will produce the results you want.
For A copy of a Project Management template you can contact us and we can go into detail and send you a copy. Implementation is a separate skill set that can take practice if you don’t have the competency so leave room for errors if you are inexperienced at implementation.
If you want to learn more about ATEEP and how to implement it apply for a discovery call now and we can do a deep dive discovery of your situation at no cost if you qualify.
Click to Apply
04/26/17 by Ankit Patel | Uncategorized | No Comments »
ATEEP is the framework that we use to help accelerate and make change stick. We’ve covered alignment in Framework for Change Management Part I and team in Framework for Change Management Part II. This post we’ll cover the first E experimentation. Before we talk about experimenting I want to first talk about the difference between learning goals and performance goals. A performance goal is a goal that most of us are familiar with. Something like I want to loose 10 pounds in 6 months, or we want to reduce defects by 5%. A learning goal would be “I want to learn nutrition science and change psychology so that I can loose 10 pounds.” Another example would be “We want to learn how to produce a better widget so that we can reduce the defects by 5%.” Th subtle difference is that we don’t assume we know he answer with learning goals. Experimenting is part of the learning process and you won’t always be succeeding. This is an important part – you will not be successful with every experiment you run.
PDCA(plan, do, check, act) or PDSA (plan, do, study, act) is a great framework for experimenting. If you are not familiar with these you can contact us and we can go into detail on how it applies to your organization and tell you if you need someone like us to help you with the journey.
It will take about 1.5-3x longer to achieve a learning goal than a performance goal because of the learning curve. Make sure you take that in consideration when planning your timelines.
If you want to learn more about ATEEP and how to implement it apply for a discovery call now and we can do a deep dive discovery of your situation at no cost if you qualify.
Click to Apply
04/19/17 by Ankit Patel | Uncategorized | No Comments »
ATEEP is the framework that we use to help accelerate and make change stick. We’ve covered alignment in Framework for Change Management Part I. This post we’ll cover T(eam) and why it’s important to the goals you want to achieve. Team refers to the people that you decide to put in charge to get the project done. When you put together a team you are not only putting technical experts but it’s important to put influencers as well. We’ve found that you need about 40-60% of the workforce involved in some way with the project to create a tipping point. It can be as low as 20% if you have the right influencers on the team but not all teams have such strong influencers.
To find your influencers you can do network analysis or just surveys and ask one question: “Who do you go to for help when you don’t know something?” That one question will reveal your informal leaders in the company. Including informal leaders will be critical to making change happen and achieving your goals.
I worked with a team who had a three shift operation and they had communication challenges between shifts. They are a multilingual plant with at least two languages spoken at any given time. We got team members from all three shifts and about 35% of the total workforce designing and creating new ways to communicate. Out of a two day event the team generated and implemented several solutions that are still being used to this date (5 years later).
If you want to learn more about ATEEP and how to implement it apply for a discovery call now and we can do a deep dive discovery of your situation at no cost if you qualify.
Click to Apply
04/12/17 by Ankit Patel | Uncategorized | No Comments »
In the last post How to Triple Your Chances of Hitting Your 2017 Productivity and Quality Goals we talked about how addressing behavior is just as important as technical changes when it comes to achieving hard goals. We used the frame work ATEEP:
A -Alignment
T -Team
E -Experiment
E -Execute
P -Permanence
For this post we’ll talk about Alignment and how it’s important. Alignment is when everyone understands clearly what need to be done and what the end goal is. An aligned team knows exactly what, how, where, when, and what they are trying to achieve and they know their role in it. They are bought in and there is little to no resistance to the goal. A good example of a team aligned is the 1980 US Olympic Hockey Team. They were not the best team or the most experienced yet managed to win Gold against overwhelming odds. They focused on conditioning and each person knew their role on the team. They were also all bought into the fact that they could win.
One of the biggest challenges is around getting everyone bought into the goal. Many times we’ll have goal the leadership team comes up with and the rest of the team had to execute. This approach can work and there are alternative ways that will get you better results when it comes to getting an aligned team.
The more you can co-create the goals with the team the better it will be when they have to take ownership and help drive the changes. One method that works well is called appreciative inquiry. It’s a way to build from past successes when creating future goals. Another way is to simply have everyone bring ideas to the table and talk through them all and validate them on their merits and a pre-established set of criteria. As a leader you want to provide guidelines and non-negotiables while at the same time provide flexibility and creativity to create the goals.
If you want to learn more about ATEEP and how to implement it apply for a discovery call now and we can do a deep dive discovery of your situation at no cost if you qualify.
Click to Apply
04/05/17 by Ankit Patel | Uncategorized | No Comments »
It’s now about four months into 2017 and hopefully you’ve made progress on your productivity and quality goals. If they are hard goals that don’t have easy answers you may have a harder time than you think accomplishing them. Most change efforts are only about 30% successful the first time. That means you have a 70% chance you won’t achieve your productivity or quality goals. If your goals seem easy to achieve and you know what it takes then this article is not for you. If there are doubts or the solution is not exactly clear then the framework we’ll talk about will help you triple your chances of success.
When we talk about hard goals,BHAG (big hairy audacious goals) we are talking about goals that are not easy. We need to address both behavioral and technical challenges. Technical meaning the “How do we calculate x” or “What is the optimal way to design something.” Behavioral is “I don’t want my job to change” or “We’ve always done it this way.” The framework that The Lean Way uses is ATEEP.
A -Alignment- get your team to all have the same goal and understanding of what is the target and why it’s important. If they are a part of the creation of the goal it helps with your odds of success.
T -Team- who is your team that you have in place to help drive the changes? You will want formal and informal influences on the team so you can have maximum impact with your workforce.
E -Experiment- leave room for mistakes and trying new things. Your first answer to your productivity and quality problems probably won’t be your final solution so leave time to play.
E -Execute- create an execution plan for the solutions that is doable and well resourced.
P -Permanence- create social capital to help cement the changes in place. Example of this are things like t-shirts, wall of fame, daily meetings, etc.
Do you follow a framework that addresses both the technical changes, behavioral changes, and the need to experiment? If no your chances of success aren’t as good as if you follow the ATEEP framework. Also keep in mind the framework is only the beginning and there are lots of nuances and details that will be important to your specific situation. If you want to learn more about ATEEP and how to implement it to improve your chances of hitting y our 2017 productivity and quality goals apply for a discovery call now and we can do a deep dive discovery of your situation at no cost if you qualify.
Click to Apply
03/29/17 by Ankit Patel | kaikaku, kaizen | No Comments »
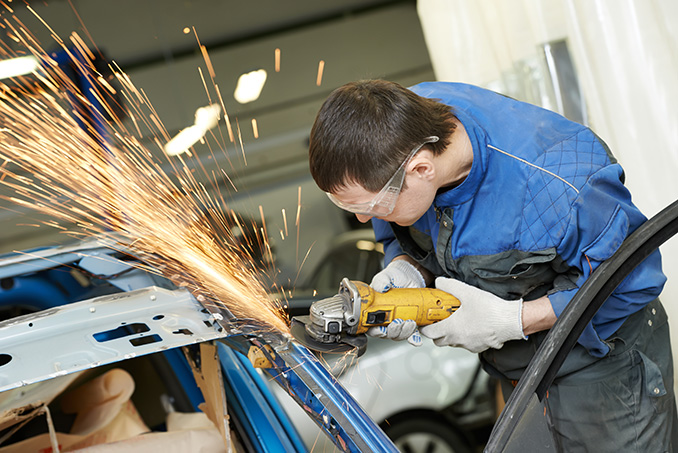
In a previous article, Lean Manufacturing Concepts and How to Use Them Part I, we talked about wastes, flow, and over burdening as core concepts of Lean. For part II we are going to look at autonomation (aka jidoka) and continuous improvement (aka kaizen) and radical change/improvement (aka kaikaku).
Autonomation/Jidoka
Autonomation or jidoka is smart automation. I way I like to remember this is “machines working for people instead of people working for machines.” This is especially important during the design phases of projects. A bad example of jidoka is when you are designing a production line and want to maximize the use of old equipment and space. You decide that you have extra parts laying around and why not take advantage of what you currently have instead of designing from scratch. This leads to you working around the existing equipment and the constraints around it. I worked on a project once where we were going to use old conveyor and re-purpose the line. We projected we would have an increase of 20% of output form this new line and we could reuse much of the equipment that already was laying around. We then went to do a Lean design and decided that we didn’t need any conveyor at all. After implementing that line we got double the productivity of the old line (aka 2x the output).
When designing with autonomation in mind ask yourself three questions 1) How fast does this item need to be produced at this station to meet customer demand. 2) How fast is the human time 3) what is the machine time. These three pieces of information will tell you exactly how much automation and people power you need to make your line flow.
Continuous Improvement/Kaizen
This is a concept that most folks in lean are familar with. Usually it’s in terms of a “Kaizen Event.” These events are anywhere from 1/2 a day to 5 days and are highly focused on implementation of improvements. Kaizen or continuous improvement in a Lean culture is also daily with daily meetings, projects, and ideas on how to constantly improve incrementally. One way this manifests is pitch tracking. Pitch tracking is when you pick a time frame where you track your production. Let’s say you want to track production hourly and you know what you should produce each hour given your staffing levels. Every hour you would see if you were short of your goal, achieved your goal, or exceeded the goal. If you were short you track the reason why you were short. After a week you sort the issues from biggest to least impact and then you create a plan to solve the biggest impact. Repeat this process until you get diminishing marginal returns on your efforts.
Radical Improvement/KaiKaku
Kaikaku or radical improvement is a lesser known concept but it’s an important one. Once you start getting diminishing returns on your continuous improvement efforts you need to shake things up. This is usually a radical transformation that changes how you do production or even a change to your business model. One example is IBM changing from a computer company to a consulting company. On an operational level this can be something like going from silo builds with cells to an assembly line that flows with feeder lines. Another radical improvement you maybe familiar with is Netflix going from buying content to creating their own content. Radical change with Lean will use processes like 3P to generate dramatic change. You can also use tools like Blue Ocean Strategy and Lean Start Up to help drive radical improvement.
By combining these concepts you can get a good starting point with Lean Manufacturing. For more information on how to implement Lean into your business you can apply for a Discovery Call on how you can implement Lean in Your Business.
03/22/17 by Ankit Patel | lean | No Comments »
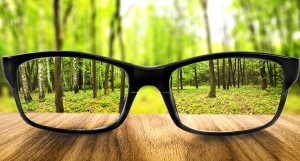
In Lean manufacturing the top three concepts you need to know about are Muda (Waste), Mura (Flow), Muri (overburdening). For why and how these three concepts became the focus of Lean Manufacturing read Is Lean Right for My Company. Waste is defined as Transportation Inventory Motion Waiting Over-production Over-processing Defects or the acronym TIM WOOD. Flow is how well a product moves through it’s path with minimal issues and as fast as possible. Overburdening refers to the people working. Are you giving them too much work and how do you know if you are? On the flip side you also want to understand how to determine value as well.
Value
Value can be defined as a process step that meets all three of these criteria:
- Does it change form, fit or function of a product
- Is the customer willing to pay for it
- Is it done right the first time
You can evaluate every step of your process with this lens to find the percentage of value add work you do at your business.
Waste
TIM WOOD is straight forward and the most used concept from Lean Manufacturing. The way you can start using this is to go to your work environment and look where you see each type of waste. Here are some examples
Transportation – any movement of a product from point A to B either internal or external to the building.
Inventory – Excess inventory. Usually you can see this if you need inventory to make sure a process stays busy. You can also see this if you end up with a lot of wasted inventory that has been sitting for years.
Motion – Think ergonomics and the motion of a person. Excess reaching or moving is classified as a motion waste. Motion refers to people and transportation refers to product.
Waiting – This can people waiting on product or product waiting on people.
Over-production – This happens when a product is produced at one station and sent on before the next station is ready for it. This usually leads to inventory build up.
Over-processing – The most common example of this is double handling. Quality inspections also fit into this type of waste
Defects – this can be process or product defects.
You can use this not only in manufacturing but in other areas like healthcare, financial industry, basically anywhere you have a process to produce a product or service.
Flow
Flow can be seen best by one metric. Time to take one product from the start of the process to the end of the process. The median time and the average time of all products gives you a good idea of how well you are flowing. To give you an idea of how long it should theoretically take a product to get through your process tag every part of the process steps as Unnecessary Waste, Necessary Waste (aka transportation), or Value. Divide the amount of time you spend on value add tasks and divide by the total task and that will give you a ratio. The higher the ratio the more “flow” you have. In manufacturing typically you have <%1 value add prior to going lean.
Overburdening
Overburdening is easy to see. Are you spending your day putting out emergencies or being proactive? The more reactive you are the more overburdening you have. The ways to address this is to standardize work content and define it more clearly. You also want to create containment plans and resolution plans for any type of reactionary event that might happen (i.e. machine downtime).
By combining these concepts you can get a good starting point with Lean Manufacturing. For more information on how to implement Lean into your business you can apply for a Discovery Call on how you can implement Lean in Your Business.
03/14/17 by Ankit Patel | Uncategorized | No Comments »
The answer is absolutely and Hell no! Let me go in to detail as to why it’s both. Lean manufacturing has a history spanning back over 100 years informally and formally since Toyota in the 1960s. It’s grown to other industries and goes by names like Lean Healthcare, Lean Government, Lean for Offices, Lean for Services, Lean IT, Lean for Financial Industry, Lean Startup, Agile, etc. In all its forms Lean is used as a way to deliver better service/products to the customer and reduce inefficiencies. At least what most would consider Lean. I want to introduce another framing and that Lean is designed to be competitive in your market.
When Toyota first started down the path of Lean they were facing a tough challenge. It was post World War II and the American companies had a large lead in the global market place on everyone else. On top of that the business was largely viewed as a commoditized business where the best way to compete was to lower costs. Lowering costs was done by selling in high volumes and leveraging economies of scale. So if you are a cash strapped company and don’t have the money to buy in bulk what do you do? If you are Toyota you look for ways to remove waste from the process and remove hidden costs. That’s where we get the seven wastes (Muda) (Transportation Inventory Motion Waiting Over-production Over-processing Defects – TIM WOOD). These seven wastes are the corner stone of what most people learn about when they learn Lean. If you have a good Lean leader they will also teach about the other ways to find hidden costs like Flow (Mura) and Overburdening (Muri). All of which are designed to give a company more cash flow to grow a business.
If you are using Lean as a way to just control costs then you will get benefits in the short run but it may not last. Lean is a Growth Strategy and doesn’t work over the long run if it’s not treated like a growth strategy. If you hope to get the long term benefits of lean it has to be a growth strategy. Many of the ways Lean gets implemented in a company is with the help of the people doing the work. If you use Lean as a cost cutting strategy then what ends up happening is that the very people that helped you get the gains end up being cut. This is because you eventually run out of other opportunities like inventory reduction. If you are growing as a company and are adding new people, technology, or equipment then there is more room for improvement.
The 2nd best way to use Lean is as a growth strategy. The best way to use it is to use the principles to be competitive in your market. One of the best way examples is Lean Startup from the software world. In the Lean Startup model it doesn’t talk about the 7 wastes. Instead the focus is on iterations of software versions and creating MVPs (minimal viable products) and testing it. The faster you can do it relative to your market then the more of an advantage you will have. This is a concept called Boyd’s Law and for more information you can see other articles I’ve written on the topic.
So the question may be not “Is Lean Right for My Company” but “What version/level of Lean is right for my company?” Here is a basic decision tree to help you with direction:
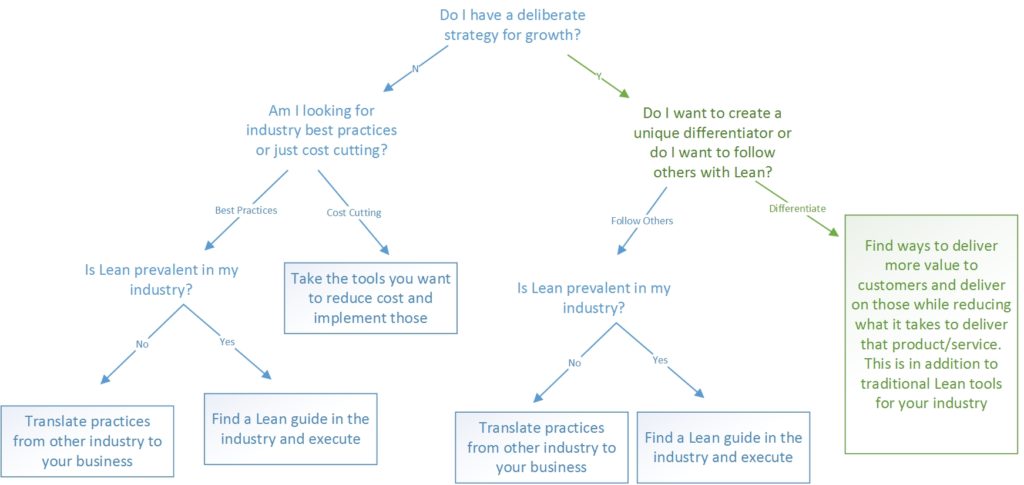
For more information on how to implement Lean into your business you can apply for a Discovery Call on how you can implement Lean in Your Business.
« Previous Page —
Next Page »